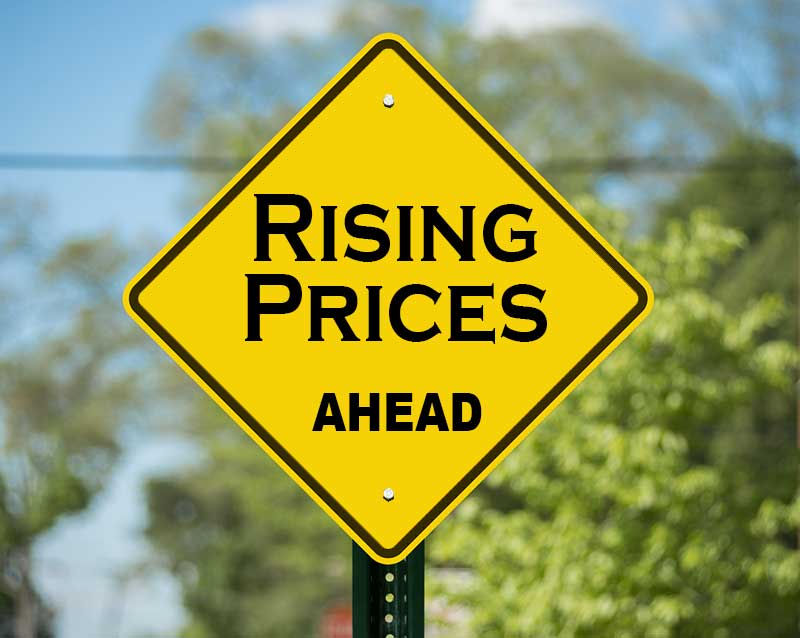
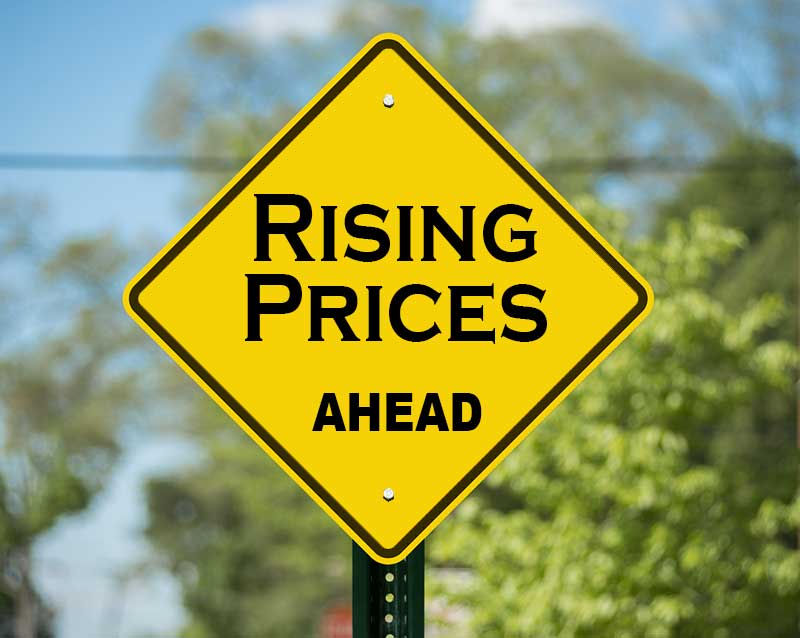
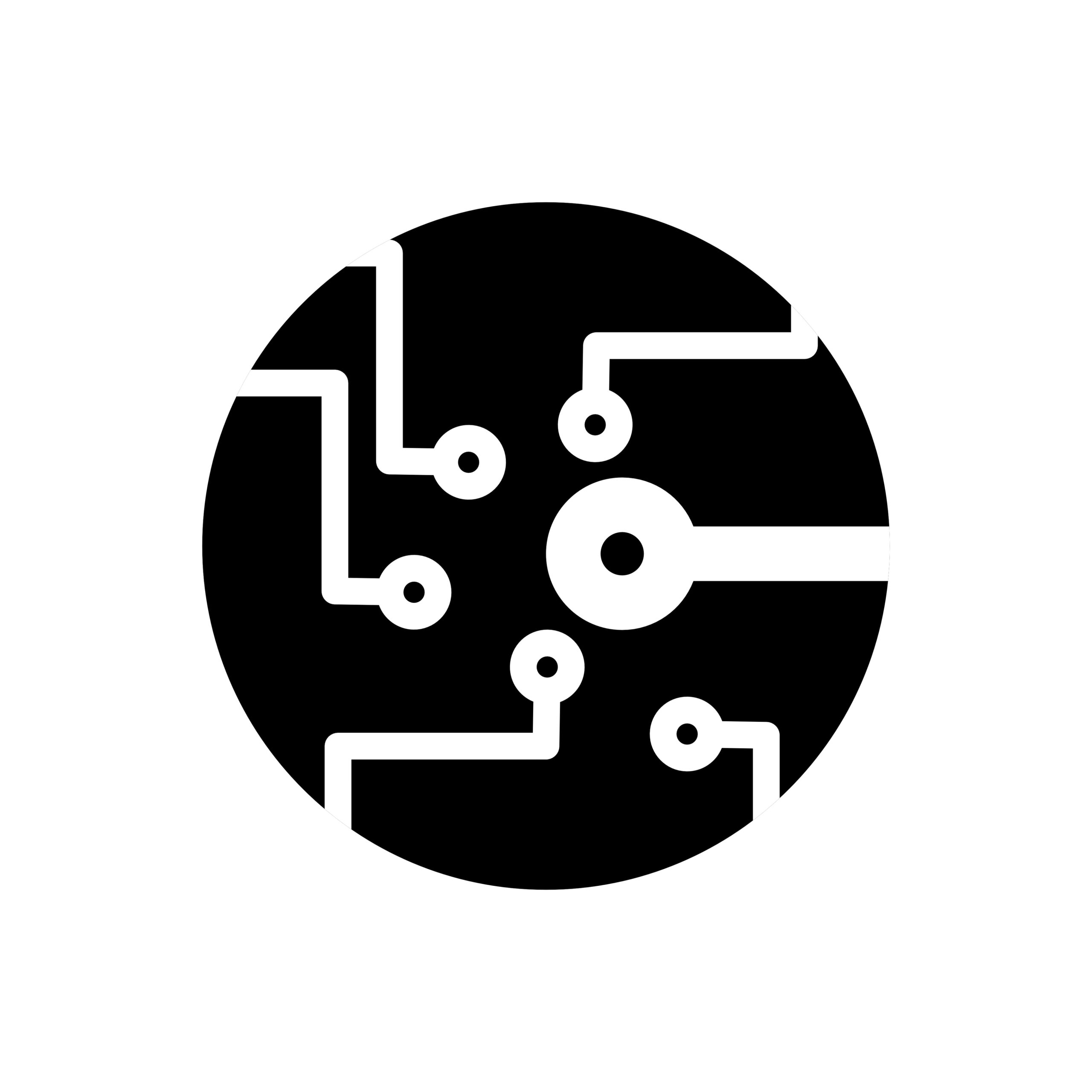
Need to revitalize your TMS? Here’s a quick and easy tip!
If you are in transportation you are probably familiar with a transportation management system, also called a TMS. Serving as the logistics central hub, the TMS helps shippers plan, execute and optimize the movement of goods with the goals of improving supply chain efficiency while strengthening customer service and compliance. While a TMS offers numerous benefits, as with any software platform, once launched there are often oversights, gaps, and missed opportunities. Many shippers believe they are stuck with what they have because there is a preconceived notion that it is difficult to modify or upgrade your TMS without consuming more resources or disrupting day-to-day business. This is simply not true. TMS Software Plugin Upgrades TMS Without Disrupting Business Software plugins can quickly and easily enhance the performance of existing software systems by adding new features and functions not available, or not required when implemented. For logistics specifically,a new innovative TMS plugin has helped transportation teams easily advance the freight procurement process by providing access to thousands of complaint carriers in seconds using AI/ML algorithms. Shippers have stated that many TMS platforms do not provide advanced freight procurement solutions, which results in shippers spending hours finding and vetting compliant carriers. They also spend time manually tracking shipments and then dealing with carrier invoicing and billing. All of these time-consuming tasks can now be automated using technological advancements. To read "Maximize Your TMS Investment" and learn more about this topic, click here.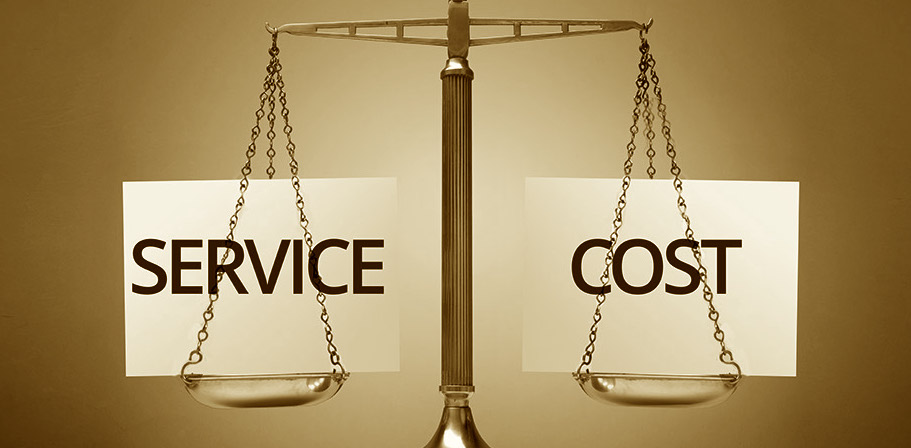
Why Transportation Teams Are Setup to Fail
Plans are just that… plans. They are never set in stone and oftentimes fall apart. The world’s best planners spend as much time- if not more- developing a strong contingency plan for when the original plan falls apart to avoid disruption. The same goes for logistics and transportation teams. The routing guide is a plan, and when executed flawlessly contracted carrier obligations are met and all loads are covered. Now imagine if flawless execution happened every time... we can dream, right? Unfortunately, we know the routing guide will fall apart. So what can shippers do today, to prepare for tomorrow? Traditional Way to Secure Spot Coverage Transportation teams are on the hook to deliver goods on time so customers remain happy while paying a fair truckload cost so expenses can be managed. Unfortunately, traditional freight procurement processes to secure spot coverage force shippers to prioritize either cost or services- not both! “Loads need to move, that’s a fact. When transportation teams are forced to prioritize cost or service they can't succeed,” said George Belle, Head of Sales Engineering at Sleek Technologies. "Both cost and service need to be taken into consideration." In the traditional freight procurement process, after a load passes contractual obligations, shippers have 2 methods to secure spot coverage: Waterfall: focused on cost, shippers connect with carriers sequentially one by one. If the carrier refuses the offer, they move on to the next in line. This process can take many hours. Broadcast: focused on time, shippers connect with all carriers at the same time. Whoever accepts the offer first, wins. The Spot Safety Net AI-powered software has advanced...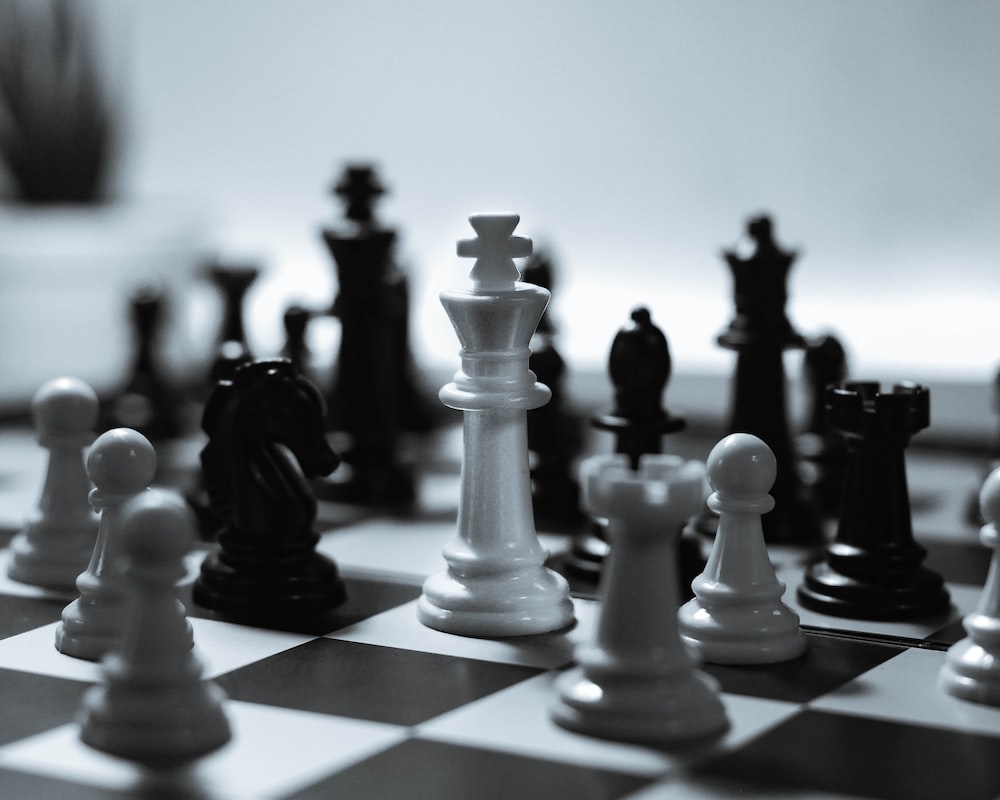
Can Shippers & Carriers Both Win in Freight Procurement? Technology Says… Yes They Can!
Freight logistics knew one truth for decades: money was a game, and someone won while someone else lost. For years, freight brokers have strategized to make the biggest amount of money they could, generally at the expense of one of the other players. The market would decide who had an advantage in each round, and that advantage was subject to change at the drop of a hat or, more accurately, at the occurrence of any disaster, legislation, or shift in the economic balance, big or small. But what if smart technology came along and advanced traditional freight procurement thinking, helping both the shipper and carrier win? Guess what…. smart technology has finally arrived! AI-Powered Freight Procurement Technology We know that technology benefits humanity by putting the world in the palms of our hands. We have the benefit of being connected, globally, to anything we want to purchase, anywhere we want to go, friends and family we want to talk to or discover, and anything we want to learn. When it comes to logistics, there is no difference. Technology instantly connects freight to compliant carriers whenever and wherever needed, so both the shipper and carrier come out on top. Technology does us the favor of removing waste. When freight brokers serve as the moderator of the game, it takes shippers hours to find, vet, and transact with new carriers. AI-powered technology dynamically matches shippers’ loads to compliant carriers in seconds using configured attributes. Only carriers who pass the pre-qualification algorithms are given a chance to bid directly on a load. With the middleman eliminated, the carrier makes more money in their...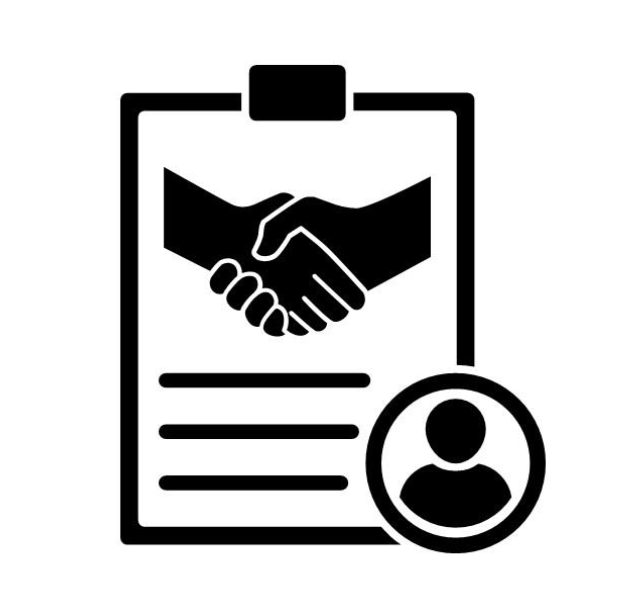
Onboard New Carriers in Seconds Instead of Hours
Freight procurement is a critical process within the supply chain. The key to success is moving goods on time while paying a fair market price, so end customers’ sales orders arrive on schedule. One of the primary puzzle pieces to freight procurement is securing compliant carriers (trucks and drivers) to move the freight. Unfortunately, the carrier onboarding process is cumbersome. According to Dean Corbolotti, VP of Managed Services at Sleek Technologies, “Onboarding new carriers correctly can take hours at best. And with everything else the transportation team has to juggle, it’s no wonder they limit the number of carriers they do business with." Finding and Vetting Carriers Finding and vetting carriers is a time-consuming process, which is required before any carrier can be added into a shipper's network. Traditionally, shippers would go to a public board and look for carriers based on specific criteria. They would dig into things like compliance, safety, accountability (CSA) scores, insurance/ liability, and operating authorities. Once a carrier passes the initial screening process, forms and data entry are required to solidify the new partnership which slows down the process even more. Automating Carrier Onboarding Updating the manual process of finding, vetting, and onboarding new carriers with automation software makes the process much faster. It goes from hours to seconds. Using a shipper’s specific load attributes, along with the carrier’s attributes, AI/ML algorithms go to work to dynamically match loads to compliant carriers. All of the onboarding leg work is done dynamically, eliminating the need for manual research. Plus with automatic daily compliance checks, shippers gain peace of mind! Expanding Freight Capacity Without automation, shippers rely...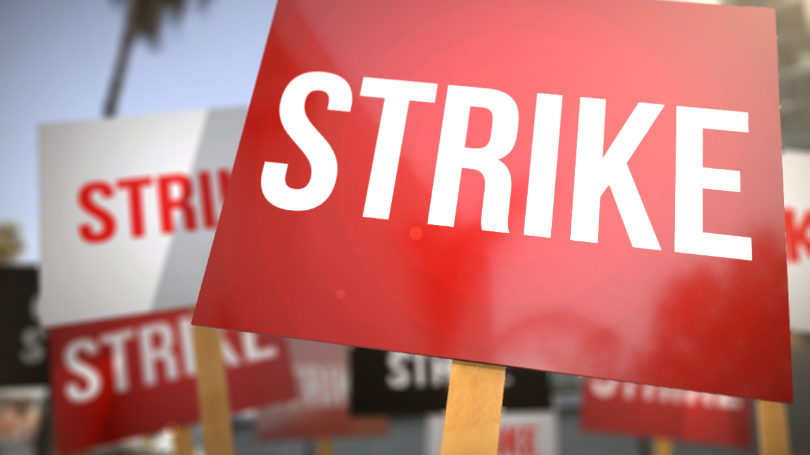
Port of Oakland Strike, What’s Next?
On November 2nd, the flow of goods was halted for several hours as hundreds of International Longshore and Warehouse Union workers walked off the job at the Port of Oakland due to stalled contract negotiations which demanded better pay and benefits. By 6 PM, dock workers returned to the ports and operations resumed. Unfortunately, this serves as yet another stark reminder that logistics is unpredictable– especially when the front line is unhappy. Dock & Warehouse Worker Threats wsws.org reported that 83% of Port of Oakland clerks (200 out of 240) have outstanding wage claims dating back to June. Arbitration isn’t possible right now because there is no signed union agreement. 22,000 West Coast longshoremen are working without a signed contract. It’s surprising that union officials have been successful in suppressing US-based strikes, dodging a major bullet on September 16th when 200 Canadian dock and warehouse workers went on strike shutting down ports in Vancouver, British Columbia. Had US workers joined the strike, all West Coast ports from Canada to Mexico would have been shut down. Fast forward to late October, when 800 Port of Mobile Longshoremen decided not to strike with promises of returning to the bargaining table. Unfortunately, West Coast issues are not isolated. Wages, benefits, job security, and safety are global issues for dock workers who have protested in Germany, South Africa, England, Canada, and Australia. Independent Truck Driver Threat In addition to longshoremen's instability, we also need to keep in mind independent truck drivers. If you recall, independent truck drivers demonstrated at LA and Oakland ports in mid-July because they opposed the AB5 legislation (reclassifying drivers as...
Should Contracted Carriers Now Be in The Hot Seat?
Heading into the end of the year usually means an uptick in carrier demand as the fourth quarter is generally the busiest time of year for most shippers. But this year, we are seeing a different picture caused by inflation and stockpiling of goods. Stockpiling & Inflation To be proactive, many merchants overstocked goods early to avoid the supply chain issues from a year ago. As we all know, last year, supply chain disruptions resulted in empty shelves, and Holiday demand that could not be fulfilled in time for Christmas morning. Retailers, manufacturers, and distributors opted to ship and hold Holiday inventory much earlier this year. So instead of huge Holiday shipments hitting the ports all at once, shipments staggered in. But that’s not the only factor. As inflation continues to make waves, analysts have agreed that consumers will purchase fewer gifts in 2022. In fact, they are predicting 9 gifts compared to 16 gifts from last year. Lower inventory that needs to be imported, combined with lower customer spending creates the perfect storm for a fourth-quarter plunge in freight capacity demand. Contracted Carrier Pricing The fourth quarter is typically the busiest time of year for shippers because of all the holiday traffic. Usually, brokers and the spot market make out like bandits this time of year, as carrier demand outweighs carrier supply. But with fewer shipments, many shippers are relying on contracted carriers to move goods. So, the key question for ALL shippers should be… “Are my contracted rates this Holiday season, aligned with true market cost”? As spot rates continue to decline, and shippers rely more on contracted...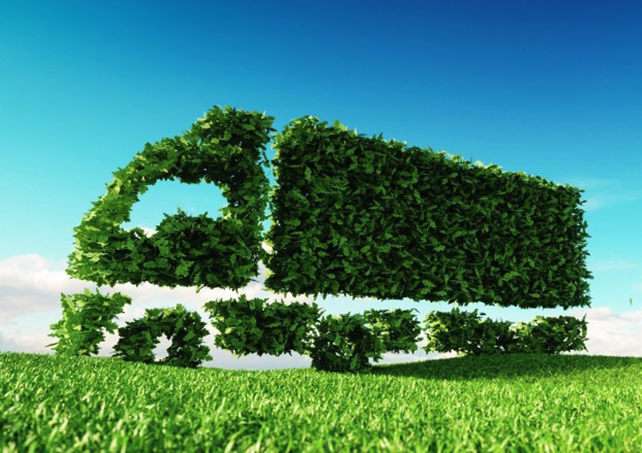
Top Tips For Over-the-Road Shippers to Build Sustainability
Did you know it is estimated that some 20 million trucks each year are mismatched to loads? And when mismatching occurs, trucks run empty on the backhaul. This is important because every time a truck moves it omits harmful carbon emissions into the air and our environment. Shippers dedicated to sustainability efforts are doing their part to ensure their loads are matched to carriers at the right time and place, so trucks run with purpose– with product. Finding the right truck, at the right time, is not as easy as it sounds, especially if a shipper still relies on traditional freight procurement processes to source capacity. Forward-thinking shippers, focused on sustainability, have completely changed their mindset on how to source capacity, and have embraced new solutions that automate the critical freight procurement process turning it from static to dynamic. Embracing AI and Freight Procurement Automation Technology With automation, AI/ML algorithms go to work to dynamically match configured shipper load attributes with compliant, asset-based carriers at the right time and place. When loads and trucks are connected at the right time, empty miles and CO2 emissions are drastically reduced making over-the-road transportation more sustainable. Sleek Technologies, the leader in freight procurement automation and an official SmartWay partner for six years running, designed their freight procurement SaaS platform [called OTS] to help shippers uncover sustainability opportunities by always matching a load with the right carrier. Without a middleman standing in between, it’s a win, win for both the shipper and carrier. Carriers reduce empty miles while shippers find the best truck for their cargo, which means they deliver on time and at a...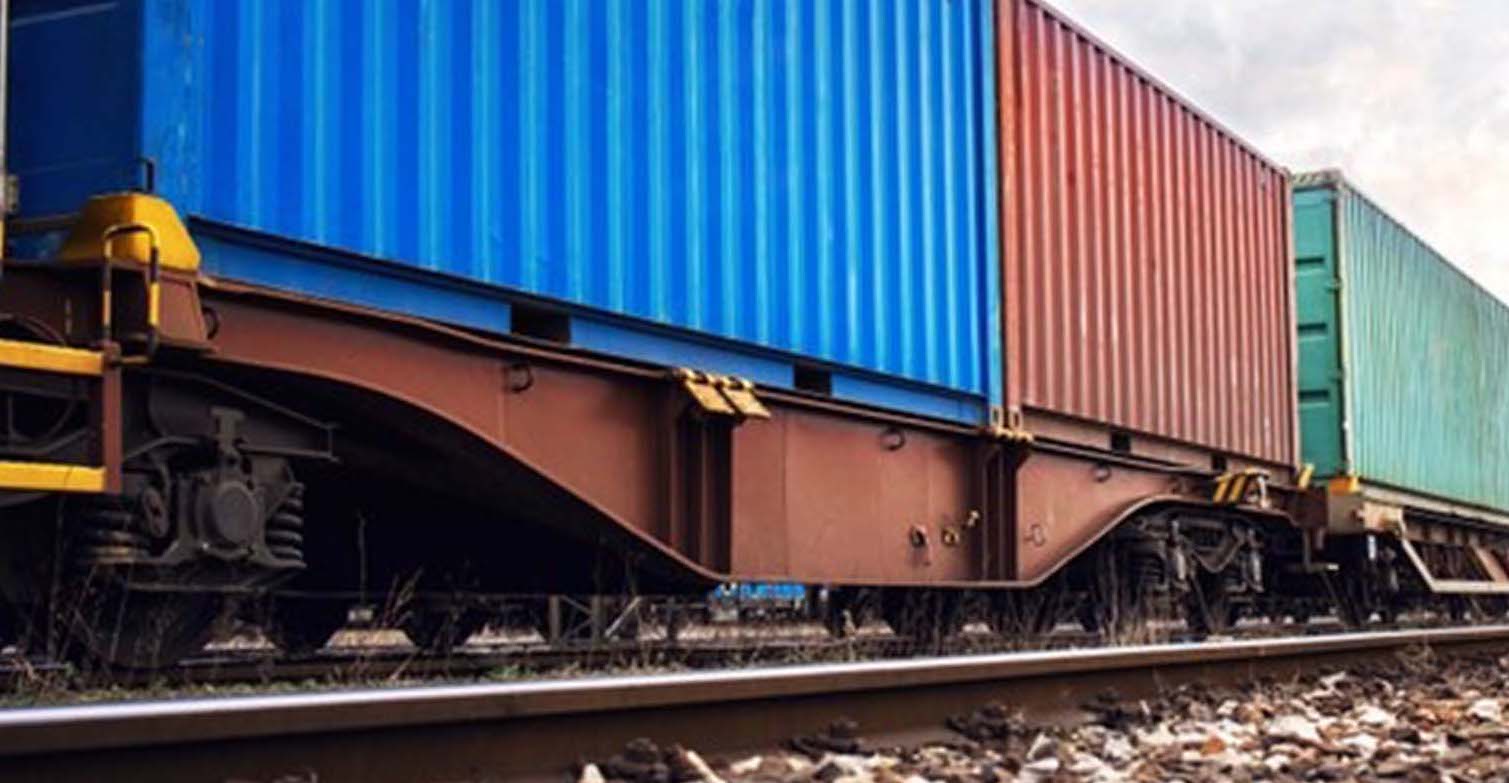
Rail Disruption Impacts Truckload Capacity & Price
For months now, the supply chain has continued to battle one issue after another. Many shippers have had to modify the way they move goods due to backed-up ports, labor shortages, and lack of truckload capacity. And rail disruption is no exception, especially off the West Coast. In fact, Alameda Corridor Transportation Authority (ACTA) reported that the share of imports hauled by rail from Los Angeles/Long Beach fell to an all-time low Jan- April 2022, dropping 40%+ YoY. And while imports dropped, the average daily number of intermodal trains serving the ports dropped from 33 in 2019 down to 27 in 2022. “Unfortunately, rail disruption is not an isolated issue”, said Michael Paul, VP Sleek Sales. “As with any mode of transportation, when disruption occurs all modes are impacted as shippers try to figure out how to keep goods moving so they deliver on time. To prove this point, DAT reports very tight capacity in LA and Abilene, TX with load to truck ratios reaching 4:1, which will cause over-road rates to increase during the fall peak season.” Congestion at West Coast ports, along with the threat of labor shortages and strikes, has led to a steady increase of trade moving away from the West Coast to the East Coast. To understand market share, one can refer to trends in container volumes. From January through May, Port of New York import containers increased 11.5% while Port of New Jersey increased 6.5%. To make matters worse, ports have begun to see an unusually early arrival of holiday products, including Christmas trees and Winter appeal. Household appliances are also part of long...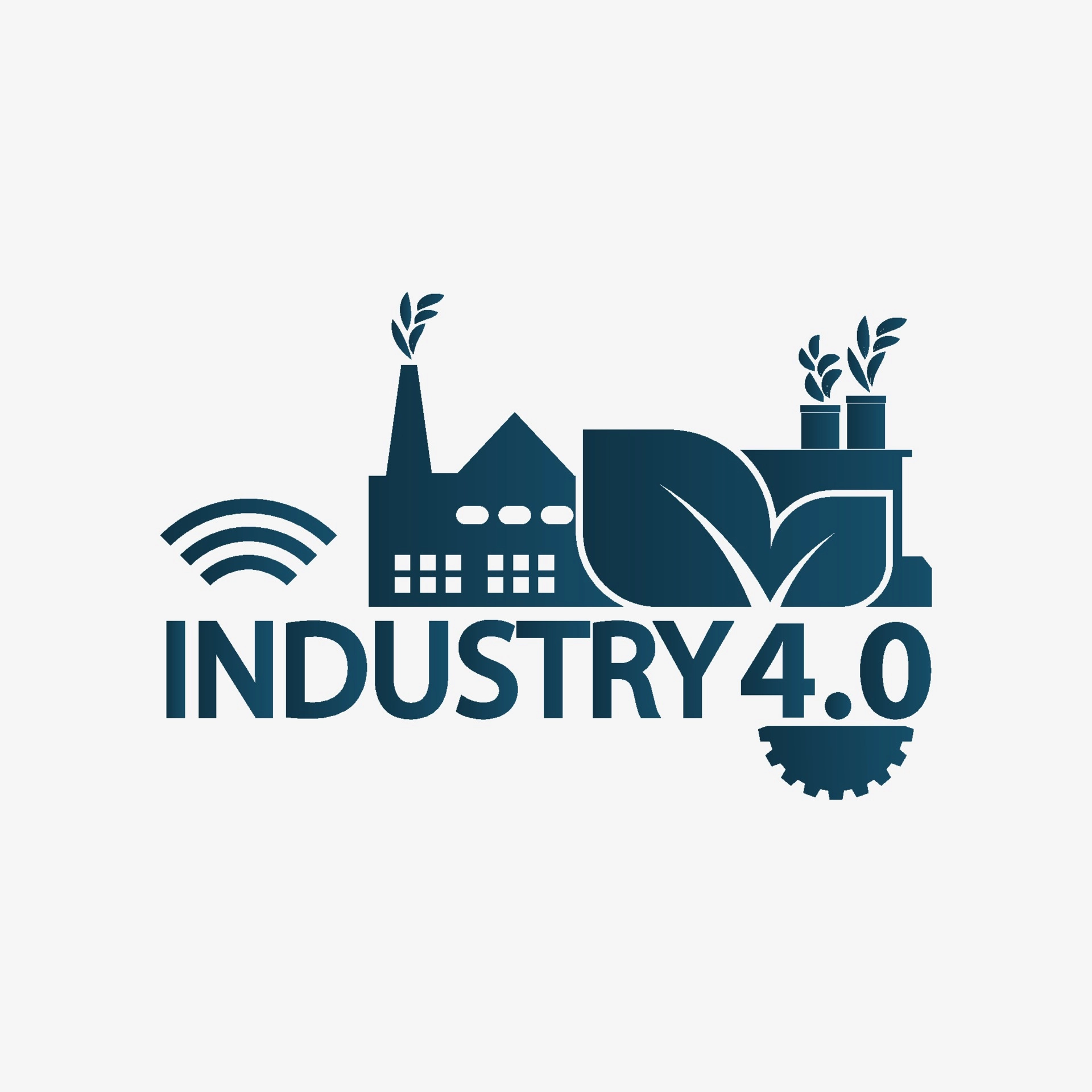