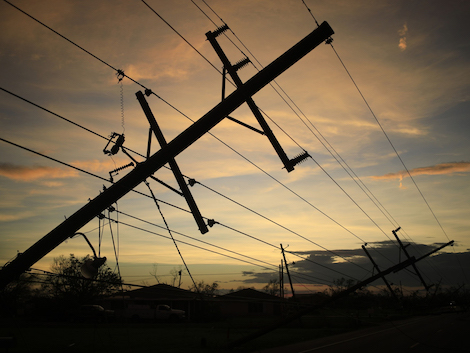
Hurricane Ida: How the Energy Logistics Industry Can Cope
Originally posted on SupplyChainBrain on 9/15/2021. This has been a devastating year thus far in terms of natural disasters, with virtually every region of the U.S. feeling the effects of some type of weather-related catastrophe. These disasters are also wreaking havoc on business, and organizations in virtually every sector are trying their best to cope with disruptions. This has been especially true for the energy logistics space in the wake of Hurricane Ida. Energy shippers are no strangers to the unique challenges of having to ship sensitive materials. Unfortunately, due to the widespread destruction of Hurricane Ida, even the most experienced energy shippers, logistics companies and freight procurement professionals are finding the situation to be incredibly imposing. With that in mind, the following are some of the challenges that Hurricane Ida is presenting to shippers in this space, and how they might be able to best navigate them. Alternative sourcing of raw materials. With hundreds of thousands of individuals without power — and even more having to evacuate entirely — many energy plants and warehouses are likely to be operating at reduced capacity at best over the coming weeks and months. This means shipments of raw materials to and from these facilities will likely be in short supply for the foreseeable future. Companies will need to expand their networks to find carriers to help meet changes and movements in production and materials sources, as they shift production from the Gulf to alternative locations. Granted, given the reduction in shipments, fuel-specific capacity will likely remain relatively open. However, trying to make such large-scale shifts in production and shipping occur can be quite hectic. Therefore, companies need...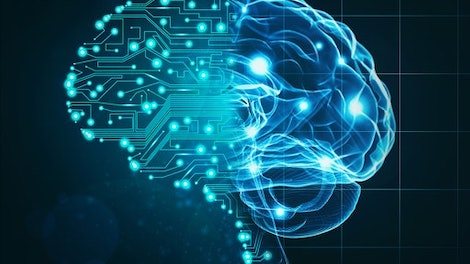
How AI is Fixing Logistics and Freight Procurement’s Data Blindspots How AI is Fixing Logistics and Freight Procurement’s Data Blindspots
Originally posted on Food Logistics on 9/24/2021. Here's how artificial intelligence helps shippers and carrier close these significant holes in their data operations and intelligence. Much like many other business verticals, the Coronavirus disease (COVID-19) pandemic has completely upended the logistics management and freight procurement spaces. And with that, many shippers and carriers are leaving no stone unturned to find inefficiencies in their operations so they can drive more revenue and cut down on waste. And, one of the biggest challenges they’re trying to overcome is the significant data gaps that exist in their operations. The logistics and freight industries are renowned for their slow technology adoption. This means that manual Excel spreadsheets, “cost-plus” calculations and other antiquated, unscientific business strategies are still widely in use industry wide. Granted, familiarity and “tried-and-true” processes have their benefits. But, by opting to stick with these old-school approaches, shippers are making their own jobs harder and effectively operating in the dark and without the data needed to make the real-time decisions that can help them reduce cost of goods and maintain their supply chain competitive edge. Luckily, artificial intelligence (AI) is helping shippers and carrier close these significant holes in their data operations and intelligence. Here are a few of the areas where the biggest data gaps exist and how AI technology is helping shrink them. Static tender process The static tender process has been a staple of freight procurement since the dawn of the industry. Unfortunately, it’s also rife with issues when it comes to data. For example, when a primary carrier rejects a shipment and it falls to the broker market, shippers...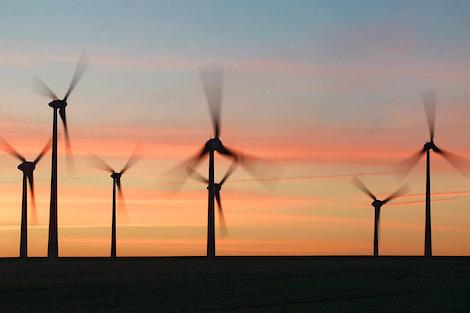
Energy Shipping Management
Energy Shipping Management Hurricane Ida had far-reaching impacts on several business sectors -- particularly on energy. Energy shippers, carriers, and freight procurement teams are no strangers to having to navigate several unique nuances and challenges given the sensitivity of what they are shipping. But the destruction of Hurricane Ida threw a whole new level of complication into the mix. With that in mind, here are a few areas in particular that energy shippers (or any shipper for that matter) need to keep in mind as the natural disaster season continues to rumble on. Higher rates Often after a disaster, freight rates will rise quite high as the market has to recoup its losses. When Hurricanes Harvey and Irma slammed the South back in 2017, spot truckload rates hit two-year highs in the aftermath. Therefore, shippers need to lean into technology and data to better predict the freight market so that they can plan for these types of disruptions should they occur. A limited supply Due to COVID, the summer shipping season, and other factors, capacity was already stretched razor-thin. Granted, given the specialized cargo, energy shippers are used to dealing in a more narrow carrier and capacity market. But when a natural disaster hits, finding capacity can be virtually impossible without the right tools in place. And unfortunately, many shippers today lack the sophisticated tech to find and lock in capacity in real-time, which would drastically help alleviate capacity woes. Safety and Reliability It is imperative that energy goods are shipped as safely and securely as possible. And unfortunately, when capacity gets disrupted en masse, it can mean that shippers need to rely on...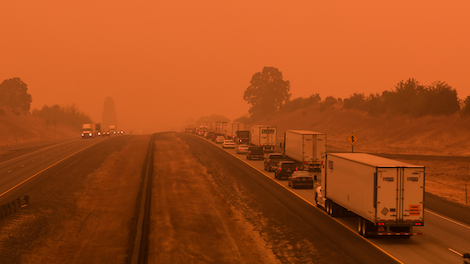
Navigating Natural Disasters: A Guide for Food Shippers
Originally posted on Food Manufacturing on 9/21/21. This year has already seen its fair share of natural disaster damage and disruptions. Here's how to alleviate some of the stress that they bring to logistics and freight procurement. From the Dixie Fire in the west to Tropical Storm Henri in the northeast, this year has already seen its fair share of natural disaster damage and disruptions. And while natural disaster management is hugely challenging for many businesses to navigate, it is particularly onerous for food manufacturers and shippers. The food industry is no stranger to the nuances of shipping sensitive and perishable items. However, when a natural disaster strikes, a new level of uncertainty enters the equation, leaving food manufacturers and shippers scrambling to cope as best as they can to meet customer demand and business goals. With that in mind, below are some quick tips for food manufacturers and shippers that can help to alleviate some of the stress that comes with trying to drive logistics and freight procurement success amid a natural disaster. Embrace Technology One of the most important steps that shippers can take when trying to become more agile and resilient is to trade in their outdated, manual processes for the more sophisticated and innovative tools that exist on the market today. Logistics and freight procurement are among the slowest moving categories in terms of technology adoption today -- with many shippers still relying on outdated methods such as Excel spreadsheets to manage their logistics infrastructure. These methods simply do not give shippers the necessary insight into their operations -- especially during periods of heavy disruption. With that in...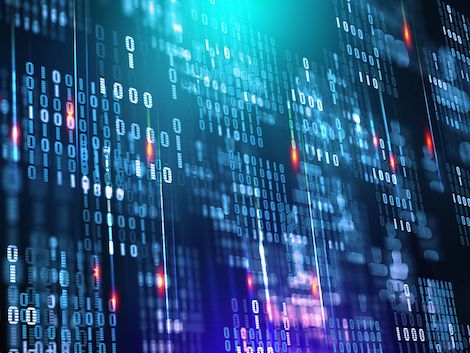
Understanding How AI is Making Freight Procurement Easier
AI is becoming a power player in logistics just as it has been in many other industries. The ability to automate the freight procurement process to positively impact key performance metrics, such as on-time delivery (OTD) is helping ease the strain for many shippers-- especially when capacity is tight! However, many shippers and procurement teams are still reticent to adopt the new technology out of “fear of the unknown”, or because they think it would be too difficult to integrate into other platforms, or simply being too comfortable with their long-established processes (even if they can no longer handle today's volatility). Here are a few reasons why shippers are falling in love with AI and why it is time for existing holdouts to take a much deeper look. Routing and Rerouting Routing is still one of the most important aspects of freighting today. But getting routing right and then adjusting routes to account for disruptions -- which happen numerous times a day -- requires a lot of legwork and time. The good news is that AI can predict what happens before it actually happens so teams can be proactive, opposed to reactive in sticky situations. AI allows teams to circumvent and/or solve problems in a fraction of time, freeing up valuable time to focus on other priorities. Optimizing the Carrier Network AI can dynamically find and match qualified, asset-based carriers when truckload capacity is needed most! It's no secret that acceptance rates are at all-time lows, which means many shippers are scrambling to find carriers to move their goods. New AI-backed technology, such as OTS Freight Procurement Software, empowers users by custom configuring over 80 load attributes so...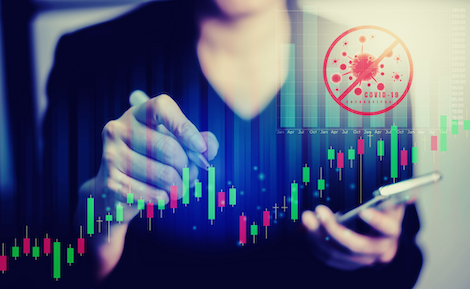