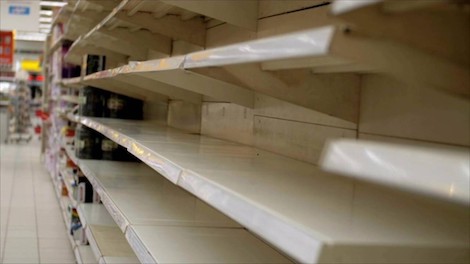
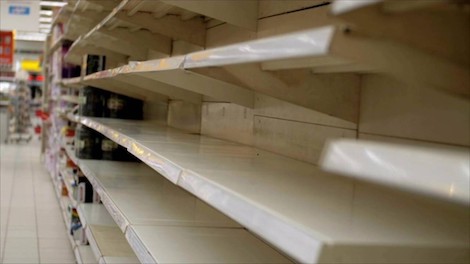
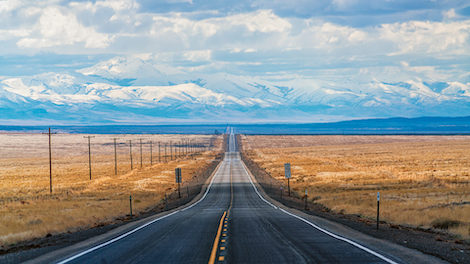
How Will Upcoming Vaccine Mandates Impact Logsitics?
Mandates for the COVID-19 vaccine have been impacting different industries in different ways, whether it’s being mandated by individual companies or by the government. The Biden administration recently set a January 4 deadline for employers with 100 or more workers to verify that all employees are vaccinated or tested weekly. And how these new guidelines will impact truck drivers has recently made headlines. Since most drivers work alone in their cabs as opposed to around other people, many truck drivers will be exempt from the mandate unless they drive with others, or interact with others at the start or end of their trip. Even with the exception, many will still be affected, which will have knock-on impacts for manufacturers, retailers, and distributors looking to haul freight. Just like the rest of the world, some drivers will comply with the mandate while others will not. Those that do not comply will either leave the trucking industry altogether or leave the large carrier in exchange for a smaller one. And as drivers leave large carriers, large carrier acceptance rates may be impacted. To keep goods moving, on-time, shippers will need to rethink their freight procurement strategy and plans, which may require shifting a portion of their freight from large carriers to smaller carriers with fewer than 100 employees. To help rethink freight procurement, and seamlessly shift to smaller carriers, shippers can use intelligent automation technology, fueled by AI and ML. This technology provides instant capacity by automatically sourcing a compliant, small carrier based on pre-configured shipper attributes. It eliminates the need for freight brokers, which are known to block small carriers from large shippers and compound issues during capacity crunches. Another...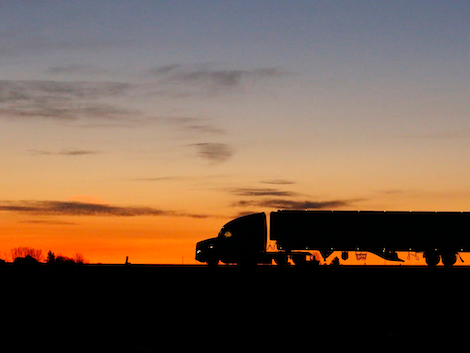
Three Tips for Improving Freight Procurement in the Supply Chain Logjam
Originally posted on SupplyChainBrain. No part of the supply chain is immune from the turmoil currently plaguing the supply chain industry — especially not freight procurement. Even when things are going well, freight procurement is critical to the success of the supply chain. But during these trying times, its importance can’t be understated. Following are some procurement-related areas for shippers to consider during this period of disruption, along with a few tips on how best to manage them. Implement modern technology tools. The the industry’s overall uncertainty has made life complicated for shippers, with pockets of open capacity cropping up unexpectedly. Today, many shippers are using outdated technology that doesn’t allow them to adapt to market changes. As a result, they may be missing the boat on less expensive procurement opportunities. Fortunately, tools like artificial intelligence and machine learning are becoming stronger and more reliable each day, providing shippers with greater agility and allowing them to respond more quickly to market conditions. In the process, they can better adapt their procurement strategies to know ahead of time when capacity becomes available. They can also optimize their expenditures and ensure that idle shipments are going out. Embrace digital transformation. Historically, logistics has been slow to adapt to changing technology. And today’s market climate is exposing just how far behind the industry is on this score. It’s common for logistics teams and shippers to be without the data infrastructure necessary to manage any disruptions that take place. And any data they do have isn’t comprehensive, since third-party procurement partners tend to operate as a reporting black box. This fragmented view of data is worsened by...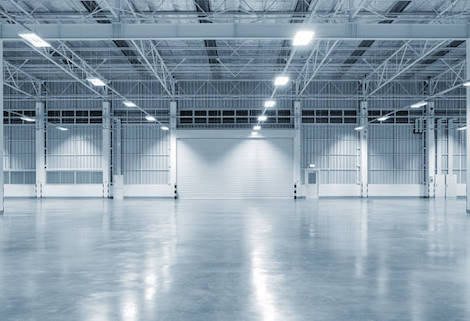